Boeing: Using Digital to Address Complexity
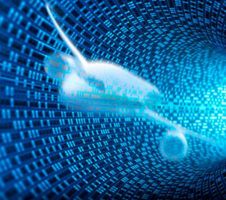
Boeing is using digital manufacturing technology to upgrade its operations and enhance American manufacturing competitiveness.
Making an Aircraft – No Small Feat
In my first TOM challenge post, I described how Boeing innovated in the aircraft manufacturing industry by delivering a totally new concept for an airplane. This feat proved to be incredibly challenging for a few reasons. First, Boeing dreamed big and envisioned a concept fundamentally different from its prior models. If we take a step back, though, we realize that another reason the project Boeing undertook was challenging was because making an aircraft is just plain hard.
Figure 1 touches on the complexity of building a Boeing aircraft; in just one year, Boeing procures 783 million parts to produce its fleet. Furthermore, these parts are sourced from over 5,000 factories.[1]
Figure 1: Boeing Supply Chain [1]
Boeing’s supply chain complexity creates operational challenges. For example, Boeing has a massive backlog of aircraft orders; in 2015, backlog orders for commercial airplanes were more than $400M. This buildup of demand puts immense pressure on lead time reduction, which Boeing is continuously trying to improve. In Boeing’s 2015 10-K, the firm states that it is producing 737’s (one if its least-complex models) at a rate of 42 per month, with hopes of increasing this number to 47 per month by 2017. Nominally the increase may seem minimal, but faster lead times enable Boeing to better meet demand and deliver millions of dollars to the top line.[2]
Using Digital Solutions to Mitigate Complexity
Boeing is using a diverse digital toolkit – tools such as augmented reality, cloud computing, internet of things (IoT), and advanced analytics – to meet both its own and its customers’ operational challenges.
Augmented Reality to Reduce Training Time
One challenge Boeing’s operation faces is that many of its production processes rely on worker know-how. As a result, training workers is imperative and often time-consuming. In an attempt to reduce training times and better document work instructions, Boeing is currently participating in an augmented reality research project through the Digital Manufacturing and Design Innovation Institute (DMDII). DMDII is a federally funded non-profit organization that focuses on developing advanced manufacturing technology and improving American manufacturing competitiveness. Boeing’s specific project intends to develop a “simple and intuitive method to quickly create augmented reality work instructions using 3D cameras with advanced image processing and computer vision algorithms.”[3] Boeing hopes to deploy this technology so that the firm can record an expert operator performing a complex process and simultaneously document the process in intuitive digital work instructions, thus reducing the cost and improving the speed of training.
Cloud Analytics / IoT to Deliver Value to Airlines
Boeing also understands that its airplanes are complex and therefore difficult for customers to maintain / service. In an attempt to reduce this service burden, Boeing has fully embraced the IoT in the 787; the 777 transmitted only 1 MB of data per flight, while the 787 transmits ~28 MB of data per flight.[4] By connecting its airplanes / sensors to the internet, Boeing is able to provide simple operational dashboards to airlines that help them save on fuel and maintenance every day. Additionally, in July 2016, Boeing announced a partnership with Microsoft intended to transition its airline solutions to the cloud, further enhancing the accessibility of these tools across mobile devices.[5]
Moving Forward
I am pleased to see Boeing using digital transformation to update its business and operating model while also taking a leading role in developing advanced manufacturing technology through organizations like DMDII. Initiatives such as Boeing’s DMDII research project not only benefit the company, but also enhance America’s digital manufacturing ecosystem and aim to reverse the trend of good-paying, advanced manufacturing job loss.
I believe Boeing should continue to enhance this ecosystem and American manufacturing competitiveness by exploring other advanced manufacturing technology. For example, airline assembly operations often are cluttered and difficult to maneuver through (see Figure 2). This environment could serve as a proof of concept for advanced robotics technology, such as the Baxter Robot from Rethink Robotics (see Figure 3). Baxter is a “smart” robot that manufacturers are using to program and perform repetitive tasks alongside workers. The robots work with humans and free up time for higher-skilled tasks. Baxter delivers bottom-line value to manufacturers, forces American manufacturing workers to learn more advanced skill-sets, and creates jobs in the Boston area (where the company is headquartered). By utilizing Baxter, Boeing could continue to address complexity with digital technology while also building on the leadership role it has taken in American manufacturing through initiatives such as DMDII.
Figure 2: Boeing Aircraft Assembly [6]
Figure 3: Baxter Robot [7]
Word Count: 760 words
[1] Boeing, “World Class Supplier Quality,” http://787updates.newairplane.com/787-Suppliers/World-Class-Supplier-Quality#, accessed November 2016.
[2] The Boeing Company, December 31, 2015 Form 10-K, https://www.bamsec.com/filing/1292716000099?cik=12927, accessed November 2016.
[3] DMDII, “DMDII Announces $12M in Project Awards,” http://dmdii.uilabs.org/press-releases/dmdii-announces-xx-million-in-research-awards-including-first-projects-in-augmented-reality-for-industry, accessed November 2016.
[4] Boeing, “The Digital Airline,” http://www.boeing.com/commercial/services/overview, accessed November 2016.
[5] Boeing, “Boeing and Microsoft Reach Agreement to Advance Commercial Aviation Analytics Solutions in the Cloud,” http://boeing.mediaroom.com/2016-07-18-Boeing-and-Microsoft-Reach-Agreement-to-Advance-Commercial-Aviation-Analytics-Solutions-in-the-Cloud, accessed November 2016.
[6] Pinterest, “Boeing”, https://www.pinterest.com/jquattrocchi/boeing/, accessed November 2016.
[7] Mathieu Belanger-Barrette, “Software Update for the Collaborative Robot Baxter,” RobotIQ, January 9, 2014, http://blog.robotiq.com/bid/69389/Software-Update-for-the-Collaborative-Robot-Baxter, accessed November 2016.
Interesting post! It’s great to see the potential digital technologies have to improve such a complex supply chain.
I wonder how these digital solutions have been implemented (piloted or rolled out at a large scale) and how Boeing will develop the necessary workforce to support its increased use of digital solutions. Will they rely largely on partnerships (like Microsoft), contractors, or will they seek to increase digital expertise in-house?
Carl – thanks for this compelling entry to your ongoing series about Boeing!
I’m particularly curious about the work that they are doing to build out an augmented reality system as a teaching aid for complex processes. This seems like an extremely high level of investment for something that only a few people will ever need to do – I understand that the training of workers is crucial to the success of the operation, but do you have confidence that an AR system is the correct approach to solving this issue? Do you believe that this effort would exist if it weren’t being funded by the taxpayers?
Maybe this is just one use-case of a scalable AR platform and they are using Boeing as a mechanism to prove the concept before they build out trainings for more common manufacturing tasks, but I’m skeptical overall. Do you share my skepticism?
Carl, great job on linking your first and second TOM challenge. Boeing has historically been plagued with problems of backlogs, as you also mentioned in your post. It is one of the main reasons it has lost out on many large orders to Airbus. While digitization and robotics will definitely act as a catalyst in improving its delivery timelines, Boeing has to be able to adopt and implement the digitization process quickly and on a large scale. It also has to focus on retaining talent and skilled workers, another one of the issues it has faced regularly.